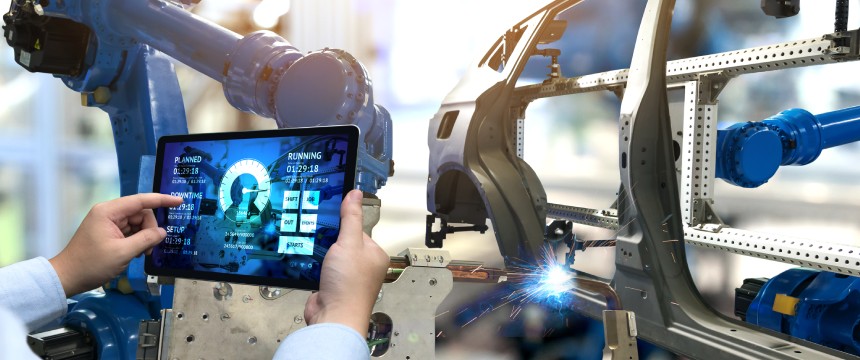
Tyson Foods plan to spend $1B to do it. Hyundai’s content at the Consumer Electronics Show this year emphasized its use in a wide variety of mobility systems. DHL’s supply chain unit doubled their use of it in 2021. Honda has stated they will invest $45B on research and development in technology areas to help develop it. Orders for it by North American companies reached $1.48B in the first nine months of 2021. The “it” is automation of the manufacturing process and, more specifically, the use of industrial robots to automate production lines. According to the International Federation of Robotics, the COVID-19 pandemic has “accelerated the use of robotics beyond established practice.”
The focus by these, and other, companies on automation does not come from a desire to replace human workers but, instead, is driven by the fact that there simply aren’t enough human workers to staff the production lines. According to a new study by Deloitte and The Manufacturing Institute, the work force development and education partner of the NAM, as many as 2.1 million manufacturing jobs may go unfilled this decade at a potential cost of $1 trillion. That may be why the Association for Advancing Automation stated recently that due to “labor shortages throughout manufacturing, logistics, and virtually every industry, companies of all sizes are increasingly turning to robotics and automation to stay productive and competitive.”
A change of this magnitude is not without operational and legal challenges. Of primary concern to small and medium-sized manufacturers is the capital expense required to deploy industrial robots. Increasingly, however, forward-thinking vendors are adopting a Machine-as-a-Service business model (“MaaS”), sometimes referred to as “robot-as-a-service.” In this model, the engineering, installation, maintenance, and support costs of an industrial robot is borne primarily by the vendor. The manufacturer pays a recurring fee for use of the robot. As we discussed in this article, vendors using this business model can track their assets and usage of their assets using blockchain technology and, further, collect payment via smart contracts supported by the blockchain data.
Legal challenges to be met include areas that some manufacturers may not be used to thinking about: data privacy and intellectual property. Because industrial robots are typically connected to local area and, in some cases, wide area networks, manufacturers making use of industrial robots and automation will want to insure that they have used a proper standard of care when protecting access to their networks and to data that may be stored by their systems. They will also want to have a response plan in place should a data breach occur. While it may initially seem that industrial robots are unlikely to store personally identifiable information that can trigger a data breach reporting event, as mass customization of products continues to grow, that possibility grows more likely.
Moreover, manufacturers will need to think differently about their intellectual property and how to protect it. Addition of industrial robots to a manufacturing line may require changes to the process that are sufficiently new and not obvious, such that patent protection is justified and desirable. Further, the operational settings and characteristics required to allow industrial robots to efficiently produce product may embody new trade secret information for a manufacturer. Protecting these new trade secrets may require changes to site visit rules, modification or augmentation of employment agreements with employees, or even renovation of the physical buildings housing the automated product lines to protect against the disclosure of such information.
Identifying legal issues presented by a proposed automation project can avoid unpleasant surprises later.